In the changing world of advanced manufacturing, the need for reliable and precise parts is greater than ever. Whether you are making parts for satellites, electric vehicle drivetrains, or semiconductor tools, your choices matter. They can affect product quality, costs, and how well the product performs in the field. Let’s explore the world of precision machining and why it’s a vital player in this landscape.
Understanding Precision Machining
So, what exactly is precision machining? In simple terms, it is a process that changes raw materials into parts.
Manufacturers create these parts to exact sizes using subtractive methods. CNC machines, lathes, and EDM systems work hard using digital blueprints. They create complex and consistent parts for important industries. When quality and consistency matter, precision machining is the best choice.
Fabrication vs. Machining: What’s the Real Difference?
While both fabrication and machining aim to create functional components, they each serve their own unique purposes. Fabrication usually means cutting, welding, and bending metal sheets into parts. Machining is about removing material to make detailed and precise pieces. It’s like two artists with different techniques, each producing masterpieces in their own right.
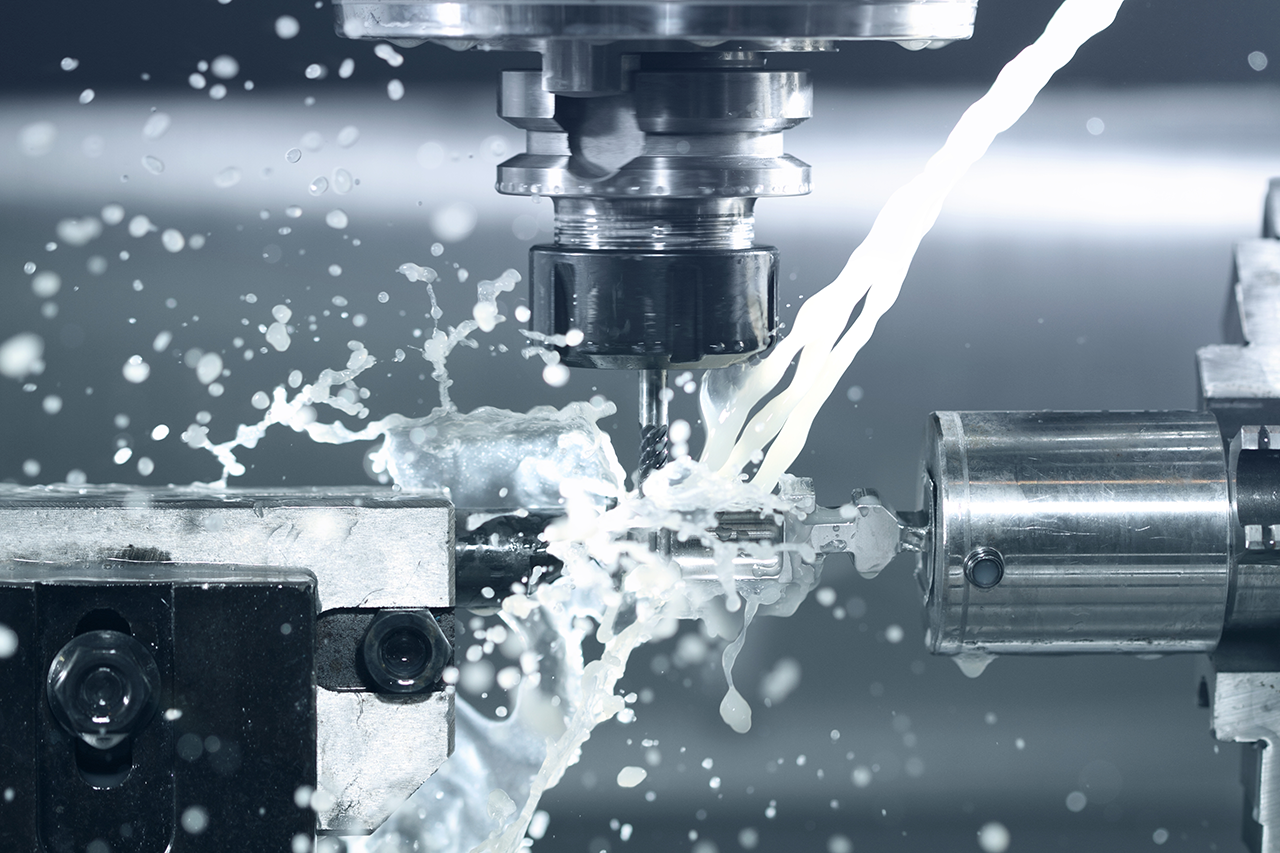
In the changing world of advanced manufacturing, the need for reliable and precise parts is greater than ever. Whether you are making parts for satellites, electric vehicle drivetrains, or semiconductor tools, your choices matter. They can affect product quality, costs, and how well the product performs in the field. Let’s explore the world of precision machining and why it’s a vital player in this landscape.
Understanding Precision Machining
So, what exactly is precision machining? In simple terms, it is a process that changes raw materials into parts.
Manufacturers create these parts to exact sizes using subtractive methods. CNC machines, lathes, and EDM systems work hard using digital blueprints. They create complex and consistent parts for important industries. When quality and consistency matter, precision machining is the best choice.
Exploring Key Techniques in Modern Machining
In modern manufacturing, the demand for consistent, top-notch output is paramount. The perks of using advanced machining include:
- Tight dimensional tolerances and a superior surface finish
- Automation that reduces labor costs
- Flexibility in handling exotic materials
- Scalability for both prototypes and mass production
- Enhanced quality control and inspection processes
Each benefit builds on the last, creating a reliable foundation for your next project.
Precision machining isn’t just a buzzword; it encompasses cutting-edge techniques that prioritize both accuracy and efficiency. Here are some of the stars in this arena:
CNC Milling and Turning for tackling complex geometries
Electrical Discharge Machining (EDM) for working with hard metals and delicate internal features
Grinding and Honing to achieve finishes and tolerances within microns
Multi-axis Machining to streamline setups and amplify accuracy
Think of it as an arsenal of tools at your disposal to tackle any challenge.
Why Precision Machining Matters in Modern Manufacturing
Meeting the Demands of High-Stakes Industries
Precision machining is at the heart of innovation and quality in today’s manufacturing landscape. Whether it’s for aerospace, defense, medical devices, energy, or semiconductor components, the demand for intricate, high-performance parts continues to grow. Precision machining techniques—especially those using advanced CNC systems—enable manufacturers to achieve tight tolerances, complex geometries, and excellent surface finishes. Compared to traditional approaches, this level of control allows for repeatable accuracy, reduced waste, and a faster time to market, making it indispensable in industries where failure is not an option.
Choosing the Right Process for the Right Project
When choosing between fabrication and machining, it’s important to understand the differences. Fabrication methods like welding, cutting, and forming are ideal for structural builds and large assemblies, while machining removes material to achieve exact dimensions and finishes. CNC machining vs. fabrication becomes a question of precision versus scale, and many manufacturers today rely on both—custom fabrication solutions for broader assemblies and precision machining for critical components. Understanding fabrication processes, materials, tolerances, and tooling selection helps engineers determine the most effective approach for quality and cost-efficiency.
What’s Next: The Future of Precision Machining
Looking ahead, the future of precision machining is driven by automation, smarter tooling, and greater integration with digital manufacturing. Innovations in the industry—like enhanced quality control systems, adaptive machining, and tighter machining tolerances—are making it easier to produce parts that meet rigorous industry standards. Whether you’re building prototypes, high-performance aerospace parts, or energy sector components, precision machining supports product reliability, regulatory compliance, and long-term performance. With the right partner, it’s not just about cutting metal—it’s about creating solutions that work, every time.
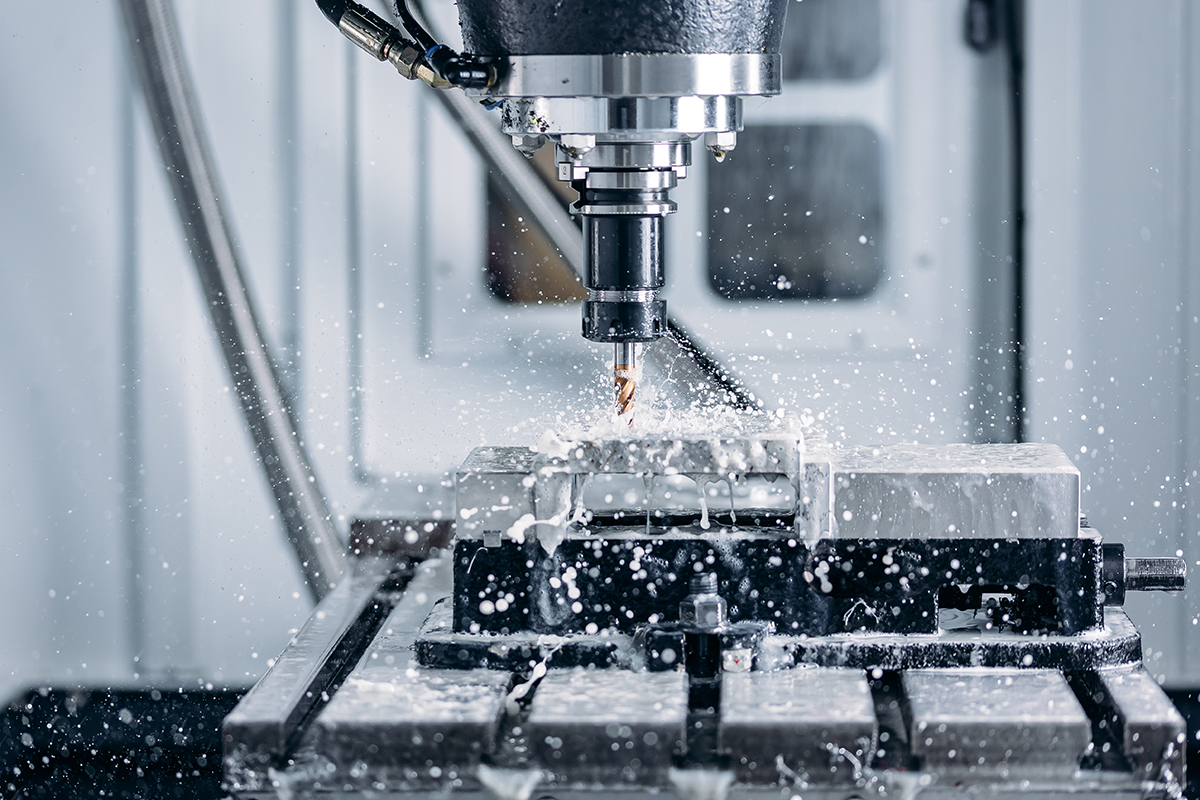
Making the Best Choice
The choice between machining and fabrication often hinges on part complexity, performance requirements, and how a material behaves. If you’re working on high-volume structural frames, fabrication might be your go-to for cost-effectiveness. For those tight tolerances and intricate designs, however, you can’t go wrong with machining.
Hear from our Partners:
For over 10 years EM2 Machine has been providing Elgin Lighting with high quality machined components. Elgin Lighting is involved in the manufacturing of explosion proof mining equipment where quality can literally mean life or death. We know we can depend on EM2 to meet our strict quality standards.